Glass and mirrors - A rich history
Glass history Part 1
5000 BC - AD 100
» The discovery of glass
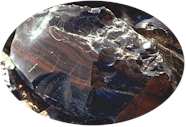
Glass probably exists since the beginnings of time, formed as a result of high temperature .... Glass history »»
Glass history Part 2
AD 100 - Industrial Revolution
» The Roman influence
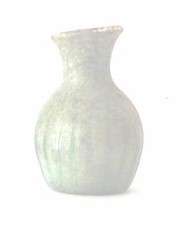
The Romans have made it possible that the knowledge of making glass could be spread so quick and in such a large area. With its conquests, trade relations, road building, ....Glass history Part II »»
Glass history Part 3
Industrial Revolution - Present day
» A craft becomes industry

It was not until the latter stages of the Industrial Revolution, however, that mechanical technology for mass production and in-depth scientific research into the relationship between the composition of glass and its physical qualities began to appear in the industry.....Glass history Part III »»
The history of mirrors

Mirrors are used by man long befor the discovery of making glass. Made of metal ....Mirror history »»
Glass and Mirrors.
The history of mirrors.
The history of mirrors dates back to ancient times when mankind first saw reflections in a pond or river and considered it magic. Long befor man was able to make mirrors out of glass, mirrors made of metal were used. Sheets of metal, mostley copper, was flattend and polished until it could be used as a mirror.
The mirror of the ancient Greeks and Romans was a disk of metal with a highly polished face, sometimes with a design on the back, and usually with a handle.
That mirrors were used in ancient times, can also be found in the bible:
Exodus 38:8
"And he made the laver of brass, and the foot of it of brass, of the lookingglasses of the women assembling, which assembled at the door of the tabernacle of the congregation."
Mirrors in ancient Egypt
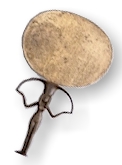
These polished bronze mirrors were used to reflect the face. They were made of molten bronze or copper. They were round, oval, square and most of the time they had a handle. If any rust developed it was easily polished new. Later in ancient Rome mirrors were made of tin, silver and even gold.
Even in present time mirrors made out of metal are being used. Just think of the laughing mirrors you can find on fairs and carnivals and traffic safety mirrors
Also small glass mirrors were used. Mirrors made of natural glass 'obsidian' with a surface as shiny as possible. Pieces of this glass sometimes were embeded in walls.
The Romans
Much later, after the discovery of glass making, the Romans made mirrors out of glass by finishing them with a metall layer.
At excavations in Germany a mirror made out of glass of 7 x 4 cm, that was covered on one side with a layer of gold that was sealed with a red shellac. In Roman graves dating from the second and third century there were also found pieces of glass covered with lead.
The Middle Ages
»mercury mirrorsAfter the discovery of glassblowing in the 14th century, mirrors were made out of glass bulbs. The glassblower blew a glass bulb that while still hot, was filled with a mixture of metalls such as lead, antimony and tin, through the blowingpipe. After cooling the bulbs, they were cut in pieces, thus forming little hollow (convex) mirrors. Although these mirrors did not have a perfect reflection, people did not mind at all. The mirrors available at that time, were made out of metall which wasn't flat and had an even worse reflection.
At the end of the Middle Ages this type of producing mirrors with liquid metalls, did evolve into the production of mercury mirrors. The metal used was in fact an amalgam of tin and mercury. A method of backing a plate of flat glass with a thin sheet of reflecting metal came into widespread production in Venice during the 16th century.
In 1507 the Danzola del Gallo brothers from Murano near Venice asked the Council of Ten:
"...the privilege for 25 years to manufacture clear and almost perfect mirrors out of crystal, unknown to the whole world except to a factory in Germany which in alliance with a Flamish factory held the monopolie in producing this type of mirrorglass....".
Therefor we can conclude that in Germany and in Belgium (Flandria) this method was already being used. The exact ingredients and procedure were kept secret for a long time, these mirrors therefor were very expensive. In 1683 the legacy of the French minister Colbert held a Venetian mirror of 115 x 65 cm, mounted in a silver frame. The mirror was sold for almost 3 times the price of a painting of Rubens, that was also a part of this legacy!
The reflecting layer of mercury on mirrors, which were made throughout a period of 400 years, existed out of 75% of tin and approximatly 25% mercury. The name 'tin mirror' therefor would be more appropriate. Technicaly spoken, it was neither one of them. The metal used was in fact an amalgam of tin and mercury.
Producing this kind of mirrors was complicated and took a lot of time. The proces was almost (there isn't an exact description) as follows;
On a stone table with a gutter along all 4 sides, a sheet of tin was placed that was slightly larger then the mirror to be made. This sheet was then secured on all sides with aggravated lathing. On the tin sheet a small amount of mercury was poured, that then was rubed in with a cloth, to ensure a connection was made. In the Middle Ages this rubbing had to be done with a hare leg. After that, a 3 to 6mm thick layer of mercury was poured on the tin sheet. All the clogging then was removed and a plate of glass was placed on the mercury. This had to be done very carefully, the plate had to float on the layer of mercury. The plate of glass then was coverd with a blanket and aggravated with weights. By removing the lathing all the redundant mercury could flow off through the gutters.
The stone table, with the mirror still on top of it, then was slantingly put for a few days, to let the last drop of redundant mercury flow off. Still slant the plate was placed on a lathing construction to dry for at least 3 weeks.
According to the description, the moment the plate of glass was lifted from the table was the most crucial moment. If there was a loud detonation anywhere near, (old literature mentions even the fire of a kanon) all the mercury would sudenly flow away, and all all the work was in vain.
Producing a mirror was a complicated and delicate process. On top of that, the production was very unhealthy, due to the fact that mercury fumes are very toxic. This type of mirrors therefor is no longer made. A passage in a very old book tells us:
"A mirror is dangerous, not only to her that reflects herself, but unfortunatly this is also true for him, who makes them. The making of mirrors therefor shall receive all the praise of mankind and the industry."
Mercury mirrors were moreover well resistant against all kinds of influences. Very old mirrors of this kind still are surprisingly well preserved. Sometimes a crystallisation of amalgam can be found on the lower part of the mirror, that side on which it stood to let the redundant mercury flow off.
19th century
»The Silver mirrorThe chemical process of coating a glass surface with metallic silver was discovered in the 19th century. This advance inaugurated the modern techniques of mirror making. Untill this day, a few country's still have a dispute about who deliverd the inventor of this process.
Most German books mention Liebig, English Drayton, the French Petit-Jean and the Italian Choron.
The German Justus von Liebig however, would be the most probable. He published an article in 1835 with the scope:
"...when aldehyde is mixed with a silver nitrate solution and heated, a reduction is formed, as a result of which the silver settles itself on the wall of the vessel, forming a superb mirror."
This chemical process forms the fundament on which later research has been based. In the course of the years many procedures have been developed and patented.
Modern fabrication of mirrors
Present-day mirrors are made by sputtering a thin layer of molten aluminum or silver onto the back of a plate of glass in a vacuum. In mirrors used in telescopes and other optical instruments, the aluminum is evaporated onto the front surface of the glass rather than on the back, in order to eliminate faint reflections from the glass itself.
The production of mirrors takes place in a production line of app. 450m. length.
"Normal" production process
The production process can be split up in to the following steps:
- loading the produktion unit with a selected high quality transparent or colored floatglass
- cleaning with ceriumoxide
chalk and water - drying - silvering with silvernitrate
- coating with copper (coppersulphate)
to protect the silver - cleaning, drying and hardening
- first coating - drying
- second layer of paint
both layers of paint protect the silver for chemical influences - cooling and cleaning
"Environmental friendly" production
The course of the process:
- loading
- cleaning and drying
- activationtreatment of the glass
- silvering
- pasivation treatment after silvering
- coating preparation
- first layer of paint - drying
- second layer of paint - drying
- cooling and cleaning
Coppersulphate is no longer used as well as leaded paint and even the ammount of ammonia salts used is much lower.
The result is a mirror that has been produced in a "environmental friendly" way.
This type of production has become more common and according to this process, there is made app. 125 million m2 of mirrorglass worldwide.